THE CULTURE OF QUALITY, ENVIRONMENT AND SAFETY
Our commitment has always been to ensure the user receives a product exactly as we formulated it
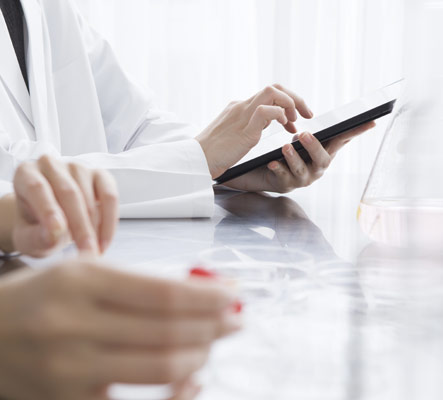
We have always pursued a fundamental genetic factor: a cross-functional quality that permeates all operational areas of the company. Attention to detail that makes the difference.
In 1996, we were pioneers in the lubricants sector, achieving ISO 9000 certification, now updated to ISO 9001:2015. This system certification attests to our control over all company processes, not as a mere certificate but as a tool to ensure the quality of what we produce for the benefit of our end customer. Over the years, the company has continued to grow, also obtaining the environmental certification UNI EN ISO 14001:2015 and the safety certification UNI ISO 45001:2018, updated in September 2023 to UNI EN ISO 45001:2023.
Our quality control is based on a rigorous selection of suppliers, evaluated through key indicators such as the quality/price ratio, completeness of technical and safety sheets, regulatory compliance, punctuality of deliveries, and technical assistance. A crucial aspect in maintaining our high technological standards is the control of raw materials, assessed for their compliance with specification documents, subjected to detailed laboratory tests, and critical analysis through warehouse sampling. Every incoming raw material undergoes careful quality control.
The mixing of raw materials represents an essential phase, where our products take shape in our production facilities, among the most advanced in the sector. Thanks to investments in Information Technology, all production processes are fully digitized, reducing human error to zero and optimizing production with a significant reduction in waste. This digitalization allows us not only to fully meet customer expectations but also to guarantee accurate tracking of all batches, with precise control of dosages and highly accurate formulations.
The finished product undergoes thorough control, assessing different indicators based on the product type, such as viscosity and density indices, to ensure the standards necessary for market release and superior performance compared to similar products. Production quality control is carried out in two ways: for strategic products or those requiring special mixing, the laboratory performs just-in-time tests directly in the mixers; for all other products, the production department verifies clarity and density, ensuring the expected quality.
All batches are inspected by the laboratory before market release.
Our commitment continues even after the sale: we constantly monitor the performance of all marketed batches, conducting daily tests on samples stored in the laboratory for over a year. Each production batch is represented by a counter-sample, initially stored in the laboratory and later in the warehouse for another two years.
Packaging and storage activities are also carefully monitored to ensure timely order fulfillment. Once ready, the product is shipped following strict quality procedures.
Product tracking is ensured by a three-level labeling system. The first label identifies the batch, production date, and any hazard warnings. The second describes the individual package, weight, and warehouse location. The third associates the product with a specific order, customer, and destination. At the time of loading, the computerized system closes the order and authorizes the printing of the transport document only if all packages have been loaded, thus ensuring maximum accuracy and traceability.